ESP32-Powered Pneumatic JCB Prototype for Construction Training
The ESP32-Powered Pneumatic JCB Prototype is an innovative project aimed at simulating the operations of an actual JCB for construction training purposes. This project leverages the capabilities of the ESP32 microcontroller and pneumatic systems to create a realistic training simulator. The primary purpose of this prototype is to provide hands-on training for prospective operators in a controlled and safe environment. This initiative aims to enhance the skill sets of operators with minimal risks and provide an educational tool for institutions offering construction machinery courses.
Objectives
1. To develop a portable and reliable ESP32-based pneumatic prototype of a JCB.
2. To create a realistic simulation environment for construction training.
3. To enhance the practical skills of operators through hands-on experience.
4. To minimize the risks associated with training on actual machinery.
5. To provide an educational tool for vocational training institutions.
Key Features
1. ESP32 microcontroller-based control system.
2. Integrated pneumatic system for realistic movement simulation.
3. Interactive control interface for user-friendly operation.
4. Safety mechanisms to prevent accidents during training.
5. Cost-effective and scalable design for mass training programs.
Application Areas
The ESP32-Powered Pneumatic JCB Prototype is an essential tool in various training and educational contexts. Primarily, it can be employed in vocational training centers and technical institutes that offer courses related to construction and heavy machinery operations. The prototype serves as a safe and effective training ground for new operators, significantly reducing the risk of accidents that are often associated with training on real machinery. Additionally, the project has potential applications in disaster management training, where precise operation of machinery in controlled environments can be crucial. It also provides a hands-on learning platform for research and development in the field of construction technology.
Detailed Working of ESP32-Powered Pneumatic JCB Prototype for Construction Training :
The ESP32-Powered Pneumatic JCB Prototype for Construction Training is an intricate assembly designed to simulate the workings of a real JCB machine, a crucial tool in construction. This prototype uses an ESP32 microcontroller to handle the diverse functionalities required for movement and control. The circuit diagram showcases the integration of various components, including relays, motors, switches, and a display module.
At the heart of the circuit is the ESP32, a powerful microcontroller known for its versatility and capability in handling multiple tasks simultaneously. The ESP32 is connected to several push-button switches, each corresponding to a specific action of the JCB. These switches form the user interface, allowing the operator to control movements such as lifting and lowering the arm, rotating the body, and operating the bucket.
To execute the movements, the ESP32 sends signals to a relay module. The relay module acts as an intermediary between the low-power signals from the microcontroller and the high-power requirements of the motors. When activated by the ESP32, the relays close their circuits, enabling current to flow to the motors. This allows the motors to perform the mechanical actions required, like rotating the body or extending the arm of the JCB.
In addition to controlling the motors, the microcontroller also interfaces with a display module mounted on the circuit board. The display provides real-time feedback to the operator, showing the status of various operations, such as which part of the JCB is currently in motion. This is crucial for training purposes as it helps the operator understand the coordination required to handle a real JCB.
The motor driver module, essential for the operation, is connected to the motors that control the pneumatic actuators. These pneumatic actuators mimic the hydraulic systems in a real JCB, providing smooth and responsive movements. The motor driver receives signals from the ESP32 and accordingly adjusts the speed and direction of the motors, ensuring precise control over the prototype’s actions.
Powering this intricate system is a power supply module that converts mains electricity to a suitable voltage for the ESP32 and other components. The power supply ensures that all components receive the correct voltage and current, essential for reliable and safe operation. Safety features are built into the power supply circuit to protect against overvoltage and short circuits, safeguarding the sensitive electronics.
The ESP32-Powered Pneumatic JCB Prototype is an excellent educational tool, providing hands-on experience in handling construction machinery. Through the detailed integration of hardware and software, operators can learn the complexities of machine movements and controls in a safe and controlled environment. The use of ESP32 microcontroller ensures that the prototype remains flexible and upgradable, allowing for future enhancements and more advanced functionalities.
In conclusion, the ESP32-powered pneumatic JCB prototype is an impressive demonstration of modern control systems applied to construction machinery training. By integrating relays, motors, switches, display modules, and a robust power supply, the prototype offers an immersive and educational experience. This innovative project not only aids in understanding machine operations but also showcases the capabilities of microcontroller-based control systems in industrial applications.
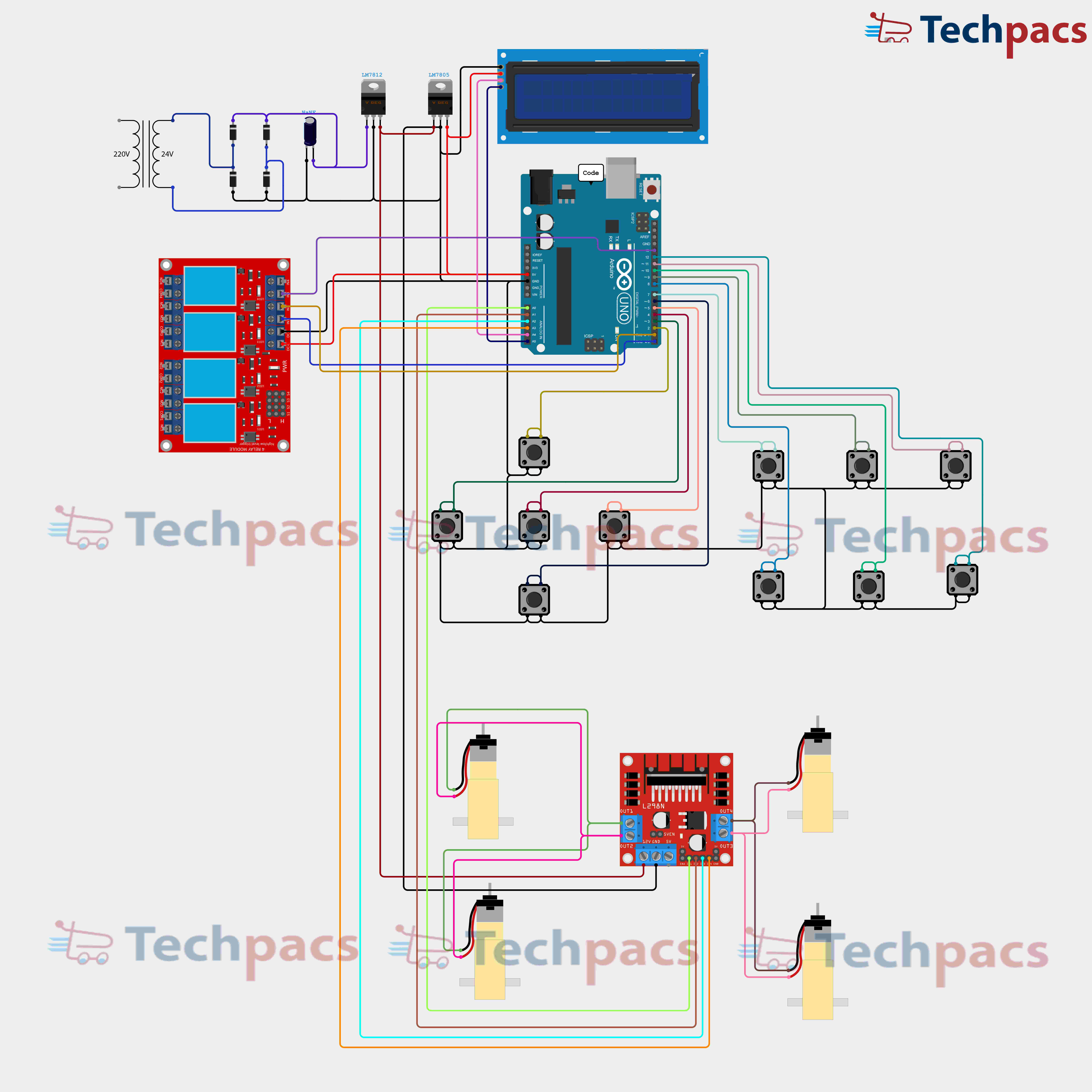
Modules used to make ESP32-Powered Pneumatic JCB Prototype for Construction Training :
1. Power Supply Module
The power supply module is critical for providing stable and reliable power to all the other components in the ESP32-Powered Pneumatic JCB Prototype. This module typically includes a transformer to step down the AC mains voltage from 220V to a lower AC voltage that is more manageable. This lower AC voltage is then rectified using a bridge rectifier to convert it to DC voltage. The rectified DC voltage is filtered using capacitors to reduce voltage ripples. Voltage regulators are used to ensure a constant output voltage, which is suitable for the ESP32 microcontroller and other components like relays and motors. This stable power is distributed to different modules to ensure their smooth operation.
2. ESP32 Microcontroller Module
The ESP32 microcontroller module acts as the brain of the entire prototype, controlling and managing the operations of other components. It receives commands from the input switches and sensors and processes these inputs to generate appropriate commands to drive the outputs like motors and displays. The ESP32 is programmed to interpret control signals for the various functionalities of the pneumatic JCB, such as arm movement, bucket lifting, and rotation. It communicates with other modules through GPIO pins, and its program determines the sequence of actions based on user inputs and predefined actions. The ESP32 is key to wirelessly controlling the prototype through possible integration with Wi-Fi or Bluetooth.
3. Input Control Module
The input control module consists of various pushbuttons and switches that act as the user interface for operating the pneumatic JCB prototype. These buttons are connected to the GPIO pins of the ESP32 microcontroller. Each button corresponds to a specific function such as moving the arm up or down, rotating the base, or operating the pneumatic actuators. When a button is pressed, it sends a signal to the ESP32, which then processes this input to determine the next action. Debouncing code is usually implemented in the firmware to ensure reliable detection of button presses without erroneous multiple detections.
4. Relay Module
The relay module serves as an intermediary between the microcontroller and the high-power actuators. It includes multiple relays, each capable of switching on and off to control larger loads. Each relay can be triggered by the GPIO pins of the ESP32, handling the high current required to operate motors or other large components. The relays effectively isolate the low-power control side (microcontroller) from the high-power operation side, preventing potential damage to sensitive electronics. These relays activate pneumatic valves and electric motors based on the control signals from the ESP32, driving the mechanical operations of the JCB prototype.
5. Motor Driver Module
The motor driver module is responsible for driving the DC motors used in the pneumatic JCB prototype. It takes control signals from the ESP32 microcontroller and provides the necessary current and voltage required by the motors. This module usually includes an H-Bridge circuit to control the direction of the motor rotation, allowing for forward and reverse movements. It allows for the precise control of the motor speed and direction required for various operations like lifting, rotating, and moving the JCB’s mechanical parts. This module ensures efficient power transfer and appropriate motor operation based on the commands received.
6. Pneumatic Actuator Module
The pneumatic actuator module includes the pneumatic cylinders and solenoid valves responsible for the mechanical movement of the prototype. These actuators are controlled by the relay module, which switches the solenoid valves on or off based on commands from the ESP32. When a relay triggers a solenoid valve, it allows pressurized air to flow into the cylinder, causing it to extend or retract. This movement mimics the actions of a real JCB, such as lifting the arm or dumping the bucket. This module translates electrical signals into physical actions, providing realistic mechanical movements for training purposes.
7. Display Module
The display module consists of an LCD or OLED screen that provides visual feedback to the operator. Connected to the ESP32 microcontroller, this display can show the current status of various parameters, such as motor positions, actuator states, and operational commands. It helps the user monitor real-time actions and provides an interface that can display error messages, operational instructions, or system status. The display enhances user interaction and understanding of the JCB prototype's functioning by providing important information directly on-screen.
Components Used in ESP32-Powered Pneumatic JCB Prototype for Construction Training :
Power Supply Module
AC-DC Converter
This component converts the incoming 230V AC to 24V DC to power the entire circuit.
Voltage Regulators
The voltage regulators stabilize and limit the output voltage to safely power other components and prevent damage.
Control Module
ESP32
This microcontroller is the core of the project, used to control the operation and logic of the entire system.
Relay Module
The relay module allows the ESP32 to control high-power devices like the pneumatic valves safely.
L298N Motor Driver
This motor driver is used to control the direction and speed of the DC motors in the pneumatic system.
Actuation Module
DC Motors
These motors physically control the movement of the pneumatic arm based on signals from the motor driver.
User Interface Module
Push Buttons
The push buttons allow the user to manually control different functions and movements of the JCB prototype.
LCD Display
The LCD display shows relevant information and statuses to the user for better control and monitoring.
Other Possible Projects Using this Project Kit:
1. Automated Plant Watering System
Using the same components found in the ESP32-Powered Pneumatic JCB Prototype, you can create an Automated Plant Watering System. The system will use humidity sensors to monitor soil moisture levels. When the soil becomes too dry, the ESP32 will trigger the relay module to power a water pump. The water pump, controlled by the L298N motor driver, will then water the plants automatically. This project is beneficial for individuals who may not be home regularly to water their plants, ensuring that plants receive adequate water and thrive. Additionally, an LCD screen can display real-time soil moisture levels, and the user can customize threshold values for optimal plant care.
2. Home Automation System
With the components provided, you can build a Home Automation System. The ESP32 can be programmed to control various household devices, such as lights, fans, or appliances. By interfacing the relay module with these devices, users can control them through a smartphone app or a web interface. The pushbuttons can be used as manual switches for the devices, and the LCD screen can provide status updates on the controlled devices. Automating household devices not only enhances convenience but also contributes to energy savings by ensuring that devices are only active when needed.
3. Smart Security System
Another intriguing project is a Smart Security System. This system can be designed to monitor doors and windows and send alerts when unauthorized access is detected. Using the ESP32, connect magnetic sensors to doors and windows to detect their open or closed state. The relay module and L298N motor driver can control alarms or automated locks. The pushbuttons serve as manual override controls for the system, and the LCD screen provides real-time status updates. This project enhances home security, giving users peace of mind by providing real-time monitoring and control over their property's access points.
4. Smart Irrigation System for Agriculture
A Smart Irrigation System could efficiently manage water resources in agricultural settings. Using humidity and temperature sensors with the ESP32, the system can monitor field conditions. The relay module, connected to water pumps and sprayers, can automate irrigation based on the sensor data, ensuring crops get the optimal amount of water. The L298N motor driver can control the movement of irrigation machinery. Pushbuttons allow for manual control, while the LCD screen displays environmental data and irrigation status. This project supports sustainable farming practices by optimizing water usage and improving crop yield.
Shipping Cost |
|
No reviews found!
No comments found for this product. Be the first to comment!